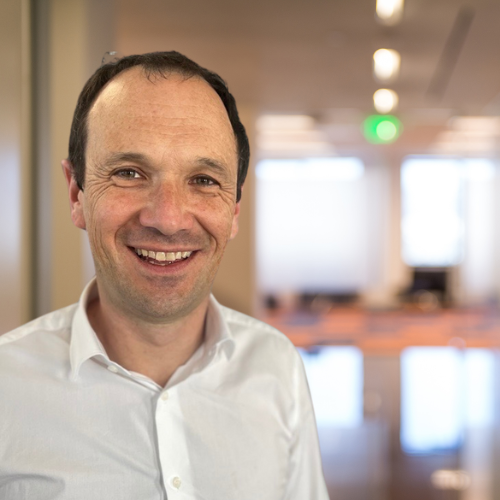
Jean-Paul Baille – Division Director
What exactly does manufacturing engineering involve in the aerospace industry?
J-P.B. Manufacturing engineering can be compared to creating a recipe in a top restaurant: the design office plays the role of the chef who imagines the dish (design stage), while we are responsible for writing the detailed recipe so that the dish can be made in the kitchen (production stage). In practical terms, based on the plans provided by the design office, we define the manufacturing and assembly solutions best suited to each part and provide technical support throughout the production process.
Additive manufacturing is one of the key drivers of manufac- turing engineering. What are its advantages?
J-P.B. Additive manufacturing makes it possible to quickly transform a design plan into a real part without resorting to complex or costly processes. Unlike traditional methods, which remove or deform material, additive manufacturing builds the part layer by layer from materials such as powder, filament or resin. It allows parts to be produced directly from a digital model (CAD), without the need for moulds or specific tools, which are often very expensive to design for small quantities. It is a fast, flexible, efficient and economical solution.
What types of projects do SEGULA teams work on?
J-P.B. We mainly work on helicopters for Airbus Helicopters, from light models such as the Écureuil to the Super Puma, including intermediate aircraft (H160, H175, NH90). We work on the structure as well as on the dynamic components and transmission systems to the propellers. Our assignments cover both new aircraft (Part 21) and those undergoing maintenance (Part 145). Whether for manufacturing or replacement, the skills required are the same: we check the technical feasibility based on the plans provided by the design office. In maintenance, we are involved in periodic inspections, major overhauls and retrofit operations, which involve dismantling an entire helicopter for modernisation.
In your opinion, what is SEGULA’s added value and what makes it unique in this field?
J-P.B. Industrialisation is part of SEGULA’s DNA, particularly through its automotive expertise. Today, we are a major player in manufacturing engineering, with an established international presence in France, Morocco, Romania and North America. These locations enable us to respond quickly to calls for tenders and reduce costs. What sets us apart is above all our comprehensive offering, which covers the entire value chain, from design to production. We also have solid experience with Airbus Helicopters, a partner with whom we have been working continuously since 2006. This longterm relationship has enabled us to develop a detailed understanding of their internal processes.
How is the Vitrolles team composed, and what profiles are you looking for?
J-P.B. The team includes both technicians and engineers, mainly with backgrounds in mechanical or aeronautical engineering, with expertise in parts design and manufacturing. Our activities cover a wide range of technical fields such as machining, sheet metal work, electrical engineering and raw material processing. It is important to have a good understanding of the logistical challenges, particularly in terms of procurement. Today, recruiting qualified staff is a real challenge because technical fields have long been undervalued, which has led to a lack of interest in these professions among younger generations. That is why we offer a training policy that enables our employees to develop their skills.
What digital tools do you use?
J-P.B. We use ERP (Enterprise Resource Planning) software such as SAP to centralise and manage all technical, logistical and production data. These databases enable us to monitor each stage of the manufacturing process with precision. In addition, computer-aided design (CAD) software, from CATIA V5 to the latest iterations of 3D Experience, geared towards MBSE (Model Based System Engineering), which is now part of our engineers’ daily routine, enables us to design, visualise and adapt parts even before they are manufactured. These digital tools have become indispensable for improving efficiency, reliability and responsiveness.