Gelatin birds catapulted onto aeroplane wings
Bird strikes pose a considerable danger in aviation. To protect against this risk, manufacturers conduct numerous tests to reinforce aircraft fuselages. This is even essential in aircraft validation processes. ‘These tests involve firing gelatin bird dummies from a catapult at a piece of fuselage to observe how it behaves,’ explains Hugo Tricou. “But these tests take time – a lot of time – and are very expensive. You also need pieces of fuselage that you are willing to destroy. It’s a huge waste! It’s much better to use digital simulation!‘ This technology involves virtually representing physical phenomena… without damaging any aircraft. ’In concrete terms, to model an aircraft part, we use the discretisation technique: it is divided into a multitude of elements (mesh), to which we apply physical laws, translated into mathematical equations.” This allows engineers to minimise testing, speed up development, reduce costs and optimise designs.
A technology tailored for aeronautics
Even more than in other sectors, digital simulation has found a privileged field of expression in aeronautics. First, because aircraft parts are very expensive. Without sacrificing safety, the aim is therefore to limit the number of destructive tests to ensure that everything works properly. Simulation is therefore key to digitally validating everything possible before moving on to physical testing. ‘Another unique feature of aeronautics is the challenges posed by the variety of materials used and their conditions of use,’ says Hugo Tricou. ‘In an aircraft, you find metals, composites and polymers that are subjected to high stresses in terms of pressure, vacuum, vibration and temperature. The more you are faced with a mix of situations, the more interesting numerical simulation becomes. Today, we know how to translate every physical phenomenon into an equation.’ The third specific feature is safety. In aeronautics, there is no room for error. Digital simulation makes it possible to anticipate all risks at every stage of development. There are no limits!
Already 25 years of experience and resources to match
SEGULA Technologies is no newcomer to digital simulation. ‘Today, we have 300 calculation engineers spread across France and abroad, and we have our own calculation servers located in our design offices, with more than 1,000 processors (CPUs – Central Processing Units) dedicated to the calculation tasks required by our customers and for our own developments, enabling us to remain at the forefront of the industry.’ These significant resources enable Hugo Tricou to serve more than 50 customers each year and handle around 30 simulation projects at the same time, in collaboration with the Research and Innovation teams. These projects have led SEGULA to achieve some real success stories. Among the most iconic is their contribution to the Lilium project. This start-up has developed the first electric aircraft capable of vertical takeoff and landing. ‘We modelled the fluid flows around the aircraft and designed a test bench using digital tools. We ensured its resistance to the strong thrusts of a vertical takeoff and the reliability of its measurements.’ Another notable example is the support provided to Safran Seats for emergency landing tests on planes and helicopters. The aim was to monitor the behaviour of the seats and assess the risks in these extreme conditions. To this end, Hugo Tricou and his team carried out rapid dynamic calculations.
A contribution to making aviation more sustainable
In addition to the applications mentioned above, digital simulation opens up endless possibilities. Not only does it reduce costs and lead times by drastically reducing the number of prototypes, limiting wind tunnel and flight testing, and accelerating iterations during the design phase, but it also enables detailed analysis of material stresses and modelling of extreme conditions. ‘In aeronautics, parts and equipment must perform perfectly the first time, while being optimised in terms of weight, robustness and defence level for military applications,’ emphasises Hugo Tricou. ‘This is precisely the role of modelling, before physical testing is carried out.’ Numerical simulation is revolutionising research into lighter parts, optimising energy consumption and studying alternative fuels such as hydrogen to reduce environmental impact: less use of raw materials and lower CO2 emissions. It also extends the service life of aircraft when integrated well upstream in the development process. When an aircraft flies for 50 years instead of 30, that’s a new benefit for the environment!
Tomorrow, simulation enhanced by Artificial Intelligence
In aeronautics, Artificial Intelligence is already integrated into processes. ‘It’s still exploratory, but it’s clearly the future,’ according to Hugo Tricou. ‘For example, it could be extremely useful for automatically generating digital meshes of parts in simulation, which is still a very time-consuming step.’ SEGULA’s Lyon design office is increasingly interested in these topics and in the use of AI to predict the behaviour of parts before they undergo conventional simulation. This is a new challenge for Hugo Tricou and his team, who are always on the lookout for innovation, as they continue to assert themselves as a key player in digital simulation in aeronautics!
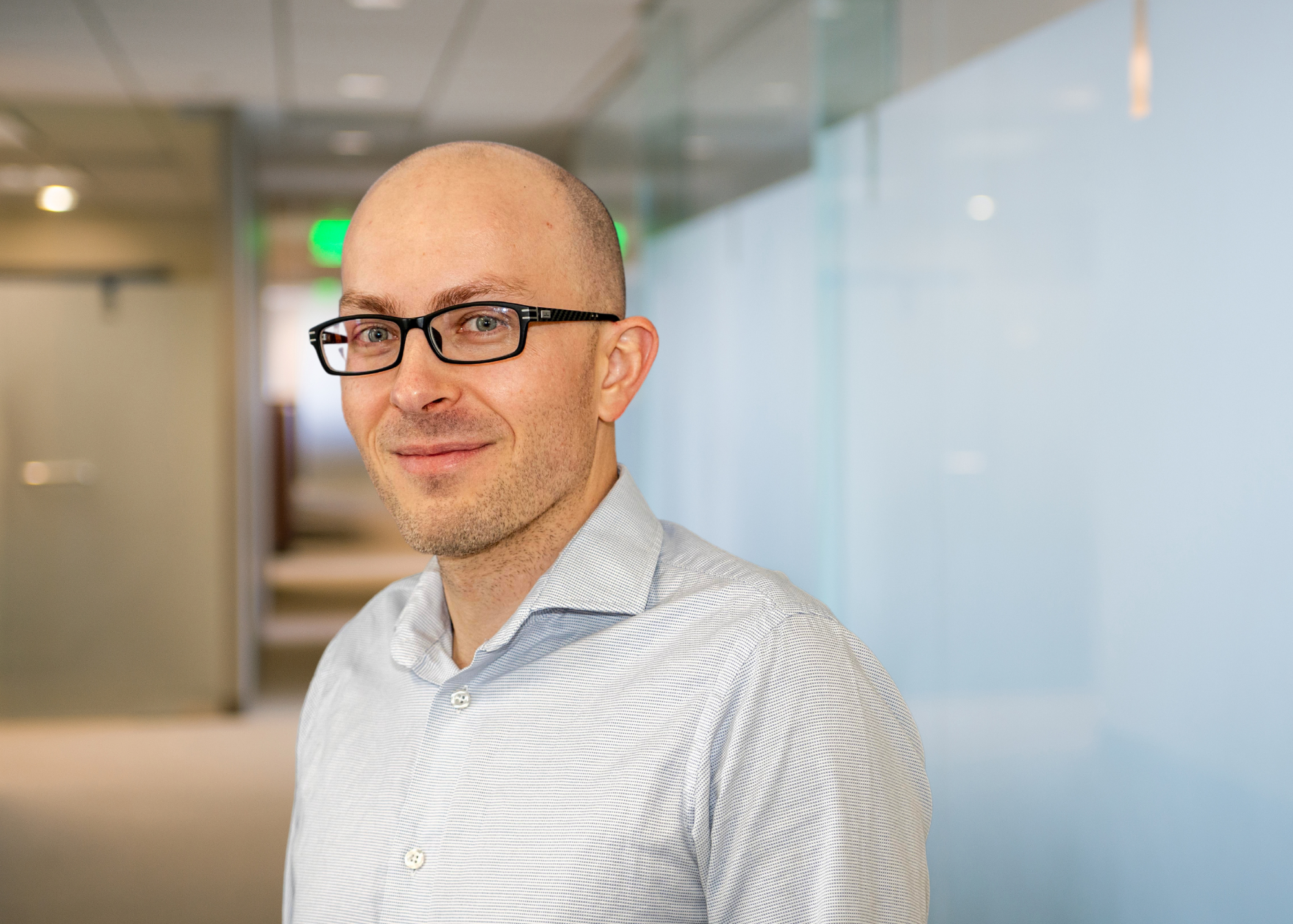
Hugo Tricou – Digital Simulation Business Manager